低碳烯烃是重要的石油化工原料,现有的低碳烯烃生产技术主要有蒸汽裂解、催化裂解、烯烃裂解和甲醇制烯烃。对这些技术特征进行分析,发现蒸汽裂解和催化裂解工艺存在着乙烯?甲烷比过低,且甲烷产率过高,而烯烃裂解工艺原料来源不足,甲醇制烯烃工艺原料主要来自煤制甲醇,造成高碳排放。现有的低碳烯烃生产技术仍有系列科学问题需要完善,为此提出靶向生产低碳烯烃的催化裂化工艺,从原料结构、催化剂活性组元和催化反应工程3个方面进行创新,深度集成现有技术,形成多产乙烯+丙烯+丁烯、乙烯+丙烯、丙烯、丙烯+丁烯4个不同的生产方案,且生产方案之间可灵活切换。
新能源及再生能源发展势头强劲,电动汽车快速发展对成品油市场带来的冲击日渐显著,汽油消费量增幅放缓,炼油能力结构性过剩日趋严重。目前最有效的化解炼油能力结构性过剩的方法就是将过剩的炼油能力部分转化为生产低碳烯烃等化学品的产能。低碳烯烃是乙烯、丙烯、丁烯总称(三烯),乙烯和丙烯(双烯)是低碳烯烃中的代表,作为单体可生产出聚乙烯、苯乙烯、聚丙烯、环氧丙烷等众多产品及中间体,是非常重要的基础有机化工原料。
乙烯产品占石化产品的75%以上,在国民经济中占有重要的地位。丙烯是总产量仅次于乙烯的一种化工原料,未来需求增速强劲。预计从2018年到2026年,全球汽油需求量复合年均增长率将低于1%,但丙烯年均增长率约4%,对二甲苯年均增长率约5%。全球化学品需求在未来10年仍将保持年均4%的增速,高于年均3%的全球GDP增速,相比之下,同期全球运输燃料需求年均增速仅略高于1%,主要原因是燃油效率的提高和非化石燃料汽车的快速发展。国内市场更是对低碳烯烃需求保持强劲的增速。
2019年我国乙烯产量25.85Mt,当量消费量51.55Mt,其中当量消费量缺口为25.70Mt,占消费量比例约50%。2019年我国丙烯产量30.88Mt,进口量3.05Mt,表观消费量33.93Mt。低碳烯烃生产主要采用蒸汽裂解和催化裂解技术。随着低碳烯烃需求量增加,出现了多种生产低碳烯烃的技术,主要有甲醇制烯烃、烯烃裂化、丙烷脱氢等技术。
从绿色碳科学观点来看,现有的低碳烯烃生产技术仍有系列科学问题需要完善:一是要进一步解决催化反应与热反应之间的矛盾,实现碳原子高效转化;二是以催化反应过程自身碳氢平衡优化实现碳氢再分布,大幅度减少干气,尤其甲烷的生成;三是精准实现C—C键断裂,提高碳原子利用效率的同时满足产品方案的变化。
对蒸汽裂解、催化裂解、轻油催化裂解、烯烃裂解和甲醇制烯烃工艺特点进行综合分析,从中发现低碳烯烃生产技术的新思路,提出靶向生产低碳烯烃的催化裂化工艺,实现C—C键精准断裂,使饱和分尽可能转化为高价值的低碳烯烃、芳香分部分转化为高价值的芳烃,同时将多环芳烃芳核保留,作为化工原料,只有胶质和沥青转化为焦炭,焦炭燃烧释放热量发汽,将蒸汽能量再转化为电能,逐步将催化裂化技术以汽油生产为中心部分转化成以低碳烯烃生产、芳烃生产和动力源为中心,促进石油化工向更高水平的绿色低碳发展。
1低碳烯烃生产技术
1.1蒸汽裂解技术
蒸汽裂解过程是指烃类原料与水蒸气混合后,在高温(750~900℃)下发生裂解生成乙烯、丙烯及其他产物的过程。蒸汽裂解的原料范围包括乙烷、丙烷、石脑油、柴油等。不同原料的乙烯收率差异很大,轻质烃类,尤其乙烷更适合作为蒸汽裂解原料。除原料性质外,工艺操作条件是影响乙烯收率的重要因素。通常可调节的操作条件包括裂解炉出口温度和压力、稀释蒸汽比、停留时间和辐射炉管构型。
总体上来说,高反应温度、低反应压力、高稀释蒸汽比和长停留时间有利于多产乙烯。从工艺条件方面考虑,蒸汽裂解发展趋势为裂解炉大型化、长周期运行、节能技术、提高灵活性和炼化一体化技术等。蒸汽裂解装置大体上可以分为反应区和分离区两个部分。目前世界上95%以上的装置在反应部分采用管式裂解炉裂解技术。分离部分根据分离的先后顺序不同可分为前脱甲烷流程(顺序流程)、前脱乙烷流程、前脱丙烷流程。
目前国际著名乙烯成套技术专利商有:美国Lummus公司、美国KBR公司、德国Linde公司、中国石油集团寰球工程公司、中国石化集团SEI公司。蒸汽裂解原料50%以上来自石脑油,25%~30%是乙烷。乙烷原料主要集中在北美和中东地区。石脑油用量最多的是亚太地区,其次是欧洲。此外欧美、亚太地区使用AGO做乙烯裂解原料的比例约占10%。
石脑油作为蒸汽裂解原料,要考虑其链烷烃含量。石蜡基直馏石脑油裂解时乙烯收率最高,如大庆石脑油是蒸汽裂解制乙烯的理想原料;异构烷烃裂解时,乙烯收率低,甲烷收率较高。终馏点在102℃以下的直馏轻石脑油,乙烯收率高,而且乙烯收率和原油种类关系不大;大于该温度后,石脑油中的异构烷烃、环烷烃和芳烃含量增加,乙烯收率下降。具有良好裂解性能的石脑油应具有较高的烷烃含量(质量分数大于65%)、较低芳烃含量(质量分数低于10%)、密度(20℃)小于0.7g/cm3、终馏点小于180℃及烯烃质量分数应尽可能小于1%等特点。表1列出国内外典型的石脑油性质及其蒸汽裂解性能。其中胜利原油及管输原油的石脑油性质最差,其乙烯收率不如大庆石脑油高。
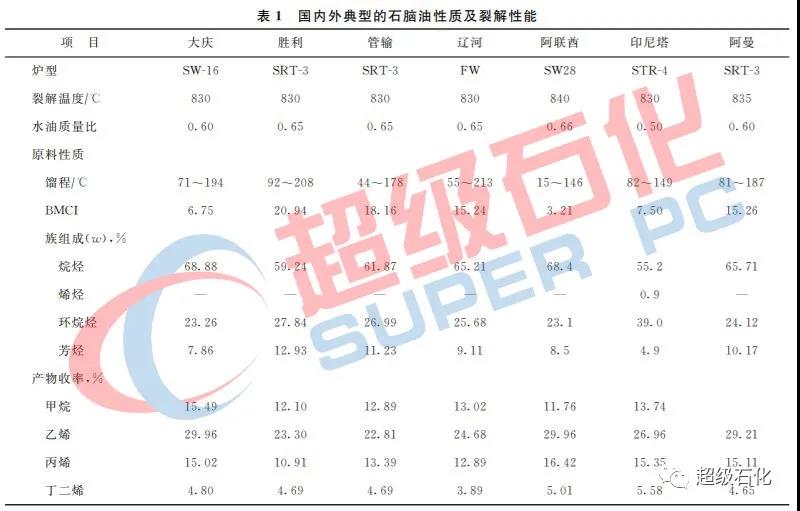
1.2催化裂解
20世纪80年代中期以来,中国石化石油化工科学研究院(石科院)致力于重油催化裂解制取低碳烯烃技术的研究,开发出以重质油(减压馏分油、焦化蜡油及渣油等)为原料生产低碳烯烃的催化裂解(DCC)工艺,原料油经水蒸气雾化后进入反应器与再生后的高温催化剂接触,反应在提升管+密相流化床反应器进行,采用专用催化剂。
以石蜡基馏分油为原料,丙烯收率超过24%,乙烯、丙烯和丁烯收率之和超过40%。加工不同类型原料的DCC装置的操作条件、产物分布及低碳烯烃收率列于表2。在DCC技术成功工业化以后,石科院又开发出由重质油直接制取乙烯和丙烯的催化热裂解(CPP)工艺,具有最大量乙烯、最大量丙烯以及兼产乙烯和丙烯等多种生产方案。相对于蒸汽裂解工艺,CPP工艺扩宽了乙烯的原料来源,降低了乙烯原料成本,同时反应温度低于蒸汽裂解工艺,因而装置能耗显著降低。2009年8月,CPP工艺已成功实现了工业化。采用大庆常压渣油作为原料,反应温度610℃,乙烷、丙烷没有回炼的情况下,在兼顾乙烯和丙烯的操作模式下,乙烯、丙烯的收率分别达到14.84%和22.21%,裂解石脑油中芳烃的质量分数达到82.46%。
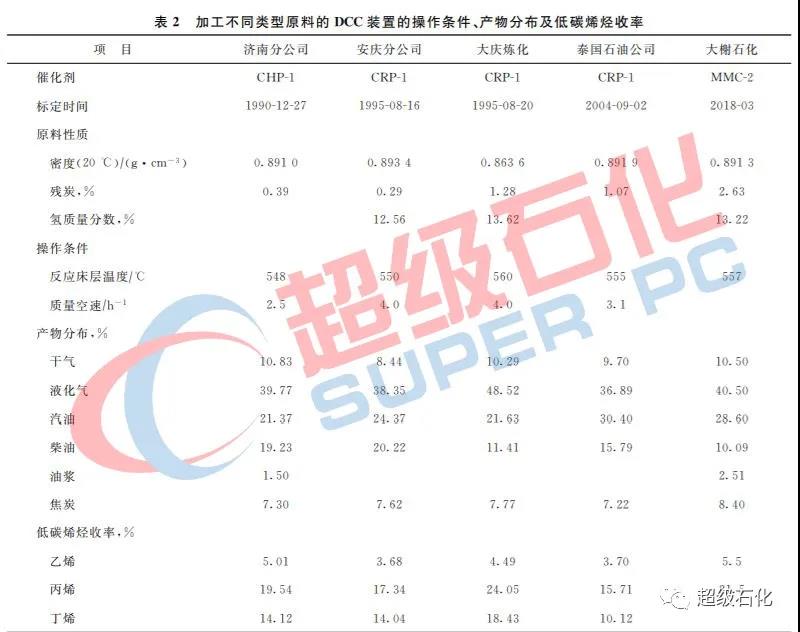
1.3轻油催化裂解
轻油催化裂解主要是指轻汽油或石脑油在催化剂存在的条件下,生产乙烯和丙烯的过程。目前石脑油裂解技术主要分为固定床催化裂解和流化床催化裂解两种。固定床催化裂解的典型代表是日本旭化成公司开发的技术,该技术以直链烷烃为原料,Mg?ZSM5为催化剂,在反应温度为680℃时,双烯收率为43%,丙烯?乙烯收率比(P?E)为0.93。流化床催化裂解代表工艺技术有韩国化工研究院和SK能源公司共同开发的ACO工艺,该工艺结合KBR公司的正流型(Orthoflow)流化催化裂化反应系统与SK能源公司开发的一种米粒状ZSM5催化剂,反应温度约650℃,乙烯和丙烯总收率提高到65%,P?E约为1。表3为典型的ACO制烯烃工艺的技术参数及产品收率。
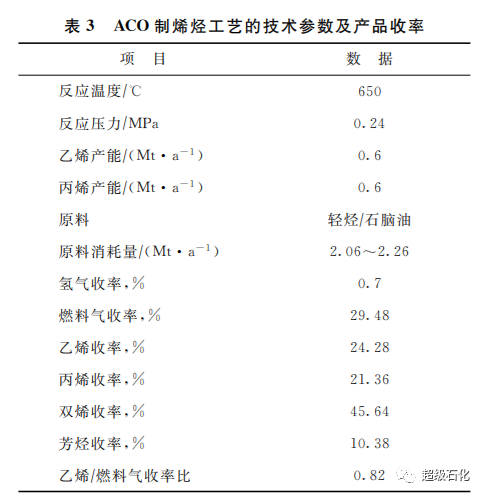
从表3可以看出,石脑油催化裂解工艺的乙烯与燃料气收率比太低,实测值只有0.82。这表明甲烷产率较高,碳氢利用率低。总的来说轻油催化裂解具有丙烯收率高的特点,对于富含烯烃原料,P?E可达到2,对于直馏石脑油原料,P?E可达到1。轻油催化裂解通常对原料的适应性强,可裂化含烯烃及醇类杂质的轻油进料包括炼油厂混合C4、FCC石脑油、延迟焦化石脑油、减黏裂化石脑油等。
1.4烯烃裂解技术
烯烃裂解技术中的代表是Atofina公司与UOP公司联合开发的OCP工艺、日本旭化成公司开发的Omega工艺、中国石化上海石油化工研究院开发的OCC工艺。OCP工艺采用专用的ZSM5分子筛催化剂,在500~600℃、0.1~0.5MPa条件下,将C4~C8烯烃原料注入固定床反应器,与催化剂接触发生催化裂解反应,反应后丙烯收率约为60%,乙烯收率约为15%,P?E约为4。
该工艺采用较高的空速,可以减小反应器尺寸,降低操作费用,且不需要任何稀释物流。催化剂再生采用切换式再生方式。OCP工艺生产方式灵活,可与蒸汽裂解和催化裂化等装置结合。当与甲醇制烯烃(MTO)装置耦合时,可在甲醇原料质量不变情况下,使乙烯和丙烯的总收率由80%提高到90%以上,丙烯收率由30%~50%提高到60%。Omega工艺采用专有的高丙烯选择性ZSM5分子筛催化剂,可以将C4~C8烯烃转化为丙烯、乙烯和C5+汽油。该工艺在温度530~600℃、压力0~0.5MPa、质量空速3~10h-1及没有稀释气存在的条件下,在固定床绝热反应器中发生裂解反应,丙烯收率为40%~60%。催化剂再生采用定期切换反应器方式。相比其他技术,Omega工艺明显提高了P?E,可达4。而传统石脑油裂解的P?E仅为0.65,如果将Omega工艺和石脑油裂解装置组合,可将P?E提高到0.8左右。
OCC工艺以全结晶复合孔ZSM5为催化剂,以绝热式固定床为反应器,采用可切换的再生器系统进行催化剂再生,在500~600℃、0.1~0.2MPa条件下,将C4?C5烯烃转化为丙烯和乙烯。原料来源主要有经丁二烯抽提或选择性加氢处理后的乙烯装置的碳四馏分,FCC或焦化装置的碳四、碳五馏分,MTBE装置的碳四馏分、MTO装置的碳四、碳五馏分。中天合创能源有限公司的200kt?aOCC装置采用MTO副产的碳四和碳五馏分作为原料,反应温度为550℃,质量空速为25~30h-1,其原料组成及产品收率列于表4。
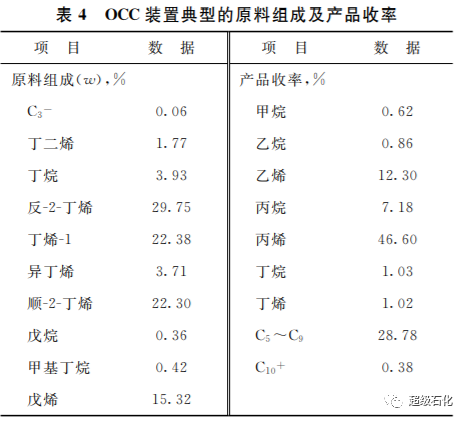
1.5甲醇制烯烃
甲醇主要由合成气经催化反应得到,而合成气可以通过天然气、煤和生物质得到,因此MTO成为石油替代工艺的一种选择。埃克森美孚公司最早提出MTO,并采用ZSM5分子筛作为催化剂进行研究,但遗憾的是后来一度放弃。随后UOP?Hydro公司对MTO工艺进行研究,开发出MTO?OCP技术。MTO技术反应部分采用快速流化床反应器,OCP技术采用固定床反应器,催化剂采用MTO100专用催化剂。
我国由于石油和天然气资源短缺,而煤炭资源相对充裕,因此MTO技术在我国得到了充分的发展,其中最具代表性的是中国科学院大连化学物理研究所(大连化物所)开发的DMTO技术、中国石化的SMTO技术和神华集团的SHMTO技术。MTO反应再生型式与催化裂化装置相似,反应部分采用流化床反应器,再生部分将催化剂烧焦再生,以保证催化剂的反应活性。分离系统与石脑油蒸汽裂解的分离系统相似,但也略有不同,主要区别在于MTO过程脱甲烷部分只需要在中低温的条件下便可进行,而传统的石脑油裂解的脱甲烷部分则需要在更低的温度下进行。各种MTO工艺路线的技术指标列于表5。
2现有低碳烯烃生产技术改善空间
2.1蒸汽裂解
蒸汽裂解工艺对原料性质要求极高,最好是乙烷,其次是丙烷、正丁烷或其他的正构烷烃。不同烷烃原料蒸汽裂解的主要产物收率列于表6。从表6可以看出:蒸汽裂解工艺最突出问题是甲烷产率过高,只有乙烷蒸汽裂解时,甲烷产率较低,乙烯?甲烷收率比达到17.40;而其他烷烃蒸汽裂解时,甲烷产率超过10%,大部分在20%左右,乙烯?甲烷收率比小于2.0,对于异构烷烃,甚至低于1.0。这表明蒸汽裂解技术加工C3以上烷烃,尤其异构烷烃,C—C键断裂的选择性严重失衡,造成石油资源利用率降低。从高效生产低碳烯烃角度来看,乙烷适合采用蒸汽裂解工艺加工,丙烷适合采用丙烷脱氢工艺加工,C4+烷烃,尤其是C5+烷烃需要开发新的技术来处理。可采用烷烃芳构化技术,将烷烃转化为丙烷和芳烃,丙烷脱氢生成丙烯,或者采用烷烃脱氢技术,将烷烃转化为氢气和烯烃,烯烃再经烯烃变换技术生成小分子烯烃。这样可大幅度地降低甲烷生成,提高碳氢利用率。
2.2催化裂解
(1)乙烯与甲烷选择性之间矛盾难以解决现有的催化裂解装置的干气产率随反应温度变化列于表7。从表7可以看出,仅靠提高反应温度增加乙烯收率,伴随着甲烷产率明显地增加,甚至与乙烯收率增加幅度相当,从而造成石油资源的浪费。也就是说,甲烷产率迅速上升,不利于乙烯收率大幅度增加,这也是催化裂解难以最大量生产乙烯的原因所在。只有催化裂解在乙烯收率上能够与蒸汽裂解竞争,催化裂解技术作为未来生产低碳烯烃的核心技术才有可能。甲烷产率随反应温度提高而明显增加,本质就是C—C键断裂的选择性失衡。
(2)丙烯选择性与重油转化能力难以兼顾对于催化裂解工艺,始终存在着丙烯选择性与重油转化能力之间难以兼顾问题。早期催化裂解工艺是在较高的丙烯选择性前提下,尽可能地改善重油转化能力。但到2000年以后,随着市场对汽油需求强劲,研究开发思路发生改变,其核心是以改善重油转化能力为前提,同时考虑汽油收率和丙烯收率,造成丙烯选择性明显降低。催化裂解装置从1990年到2020年产物分布、丙烯收率以及丙烯含量充分证明这一点,具体见表8。从表8可看出,在原料油性质基本相当的情况下,AQ催化裂解装置2020年丙烯收率更低,即使反应温度提高20℃,丙烯收率只有13.50%;丙烯在液化气中含量更低,质量分数只有39.10%。相对于早期1990年催化裂解装置的丙烯在液化气中质量分数为49.13%,降低约10百分点以上,导致丙烯收率减少超过6百分点,创这套装置开工25年来历史最低水平。由此可以看出,以改善重油转化能力为前提时,催化裂解技术在丙烯收率和选择性上处于大幅度退步中。只有恢复到早期催化裂解开发思路,以较高的丙烯收率和丙烯选择性为前提,方可促进催化裂解技术进步。
2.3其他烯烃生产技术
轻油催化裂解工艺的反应温度较高,反应由自由基机理和正碳离子机理共同作用,C—C键很难选择性断裂,同时轻油原料的主要组分为烷烃,导致其主要问题也是乙烯?甲烷收率比低,且乙烯和丙烯收率低。为了强化正碳离子机理作用,催化剂多采用酸性材料,苛刻的反应条件对催化剂的要求也更高,使投资成本相对较高。石脑油催化裂解工艺的乙烯收率低于蒸汽裂解,而燃料气收率高于蒸汽裂解。基于现有的石脑油催化裂解工艺指标评估,可知其市场竞争力较差。烯烃裂解技术的主要限制是烯烃原料来源不足。
目前所使用的原料主要来自于C4烯烃,碳数更高的烯烃还承担着调配汽油池辛烷值的重任,且烯烃和烷烃的分离存在困难,导致此类技术无法大规模应用。在现有烯烃裂解技术的条件下,反应在酸性催化剂上发生,形成的正碳离子通过!裂解断链,导致丙烯收率较高,而乙烯收率难以提高。
虽然MTO工艺在反应研究和催化剂设计上取得了重大突破,工艺过程也在不断地完善。甲醇制烯烃技术需要足够的甲醇原料,装置规模应该在1.80Mt/a更为经济。我国能源结构决定了我国的甲醇原料以煤为主,目前我国超过70%的甲醇来自于煤。从投资成本来看,煤经甲醇制丙烯的装置成本相对较高,约为石脑油蒸汽裂解的两倍,项目投资建设周期较长。
同时,以煤基为原料的MTO工艺十分复杂,且产生的合成气缺乏氢气,造成碳效率偏低以及水资源消耗偏高。据估计,这些装置生产每吨烯烃所排放的CO2在6~10t之间,而裂解工艺只有1t左右,碳排放强度太高,不符合国家所提倡的碳中和要求。从降低碳排放角度来看,甲醇来源最好为生物质、电解水制甲醇。如果是这样,甲醇原料可能是非连续性的、小规模的,由此要求加工装置适应这样的原料特点。
3靶向催化裂化技术开发思路
3.1现有低碳烯烃生产技术特点及启示
综上所述,蒸汽裂解、催化裂解、轻油催化裂解、烯烃裂解和甲醇制烯烃技术特点汇总列于表9。
3.2试验探索
基于表9给出的启示,选择戊烯作为原料,中孔沸石作为催化剂活性组元,在固定床装置上进行探索试验,结果见图1和图2。
3.3烯烃催化裂化与烷烃蒸汽裂解技术对比
蒸汽裂解工艺加工原料主要是小分子烷烃,而靶向催化裂化(TCO)工艺中的烯烃裂解反应主要处理小分子烯烃。为此,选择戊烷蒸汽裂解与戊烯靶向催化裂化来评估两个工艺技术性质的差异,结果见表10。
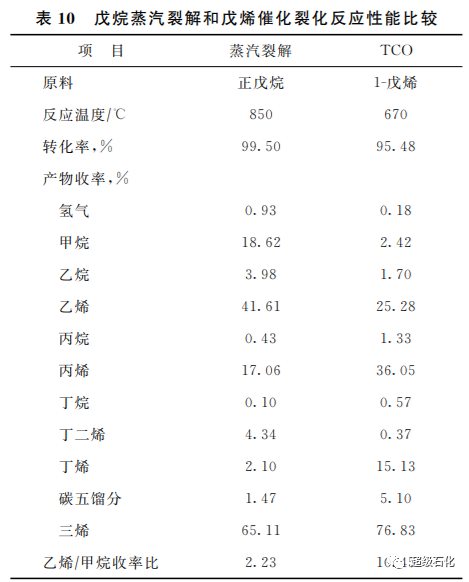
3.4烯烃原料来源
小分子烷烃来自石脑油、重整抽余油和轻质烃,这些烷烃经烷烃脱氢装置处理后,生成氢气和烯烃,烯烃输送到TCO装置,可作为生产低碳烯烃的原料。减压馏分油、加氢重油、常压渣油直接作为TCO装置原料,先进行催化裂化反应,尽可能地生产烯烃,然后将烯烃从产物中分离出来,返回到TCO装置反应器的烯烃裂化区。甲醇、乙醇等醇类也可以作为TCO装置原料,注入反应器合适部位,转化为低碳烯烃。以加氢蜡油为原料,其密度(20℃)为0.892g/cm3,氢质量分数为12.85%,在小型流化床试验装置上进行靶向催化裂化试验,试验结果列于表11,同时列出相同性质的原料油催化裂化(MIP)和催化裂解(DCC)小型试验结果。
从表11可以看出,与MIP相比,TCO工艺的液化气烯烃收率增加12.61百分点。在3种技术中,TCO工艺的产品丙烯?丙烷收率比和异丁烯?异丁烷收率比最大,液化气烯烃度也最高,达到83.0%,说明TCO工艺能更好地将原料分子靶向裂化成所需高价值的低碳烯烃,且焦炭产率仅为1.99%,干气产率仅为2.25%,其中甲烷产率低于1.0%。因而TCO技术可明显地提高碳原子的利用率。DCC工艺和TCO工艺的烯烃收率都约为41%,产品烯烃分布如图3所示。考虑DCC工艺转化率为85.6%,而TCO工艺转化率为64.11%,由此可以算出TCO工艺烯烃选择性明显地高于DCC工艺。这充分说明TCO工艺高效地将原料中的饱和烃分子转化成烯烃产品。将产品烯烃经分离循环至反应器的烯烃裂化区进行再裂化反应,靶向生产乙烯、丙烯或丁烯。除此之外,相对于MIP和DCC工艺,TCO工艺更关注低碳烯烃在扩散过程中限域催化的有效性,维持所生成的丙烯和丁烯在扩散过程中较少地转化为丙烷和丁烷。
烷烃原料通过烷烃脱氢工艺制取小分子烯烃,减压馏分油、加氢重油、常压渣油首先经TCO工艺进行预处理制取小分子烯烃,再加上其他装置所生产的烯烃,还有含氧化合物。因此,靶向催化裂化工艺原料来源充分,如图4所示。
4.TCO技术概念设计
4.1靶向催化裂化工艺流程及进料位置选择
靶向生产低碳烯烃的催化裂化工艺从原料结构、催化剂活性组元和催化反应工程3个方面进行创新,深度集成蒸汽裂解、催化裂解、烯烃裂解和甲醇制烯烃技术,形成单一的生产低碳烯烃技术,完善了现有的生产低碳烯烃技术系列科学问题,主要表现在:一是以反应过程自身碳氢平衡优化实现碳氢再分布,大幅度减少小分子烷烃,尤其甲烷的生成;二是精准实施C—C键断裂,在提高碳原子效率的同时满足低碳烯烃生产方案高效灵活切换。基于戊烯靶向催化裂化探索试验结果,反应温度超过650℃时,乙烯和丙烯收率明显增加,而低于650℃时,丙烯和丁烯收率较高。催化裂化工艺热再生催化剂进入反应器底部与新鲜重质原料接触区域的温度在650℃以上,正好满足富含烯烃原料裂解为乙烯和丙烯对反应温度的要求,热再生催化剂与新鲜原料接触后,反应温度快速降低,至反应器扩径处温度一般控制低于530℃,此处满足富含烯烃原料裂解为丙烯和丁烯对反应温度的要求,到扩径段中上部,反应温度可以控制得更低,满足醇类裂化对温度的要求,由此可以设计出靶向催化裂化工艺基于进料位置差异所形成的4个不同的生产技术方案。乙烯+丙烯+丁烯生产技术方案进料位置分布见图5(a),乙烯+丙烯生产技术方案进料位置分布见图5(b),丙烯+丁烯生产技术方案进料位置分布见图5(c),丙烯生产技术方案进料位置分布见图5(d)。基于市场对低碳烯烃类型的需要变化,可调整富含烯烃原料进料位置,实现生产方案之间灵活切换。
4.2靶向催化裂化装置在未来炼化一体化流程中位置
靶向催化裂化技术一旦开发成功,其装置将处于炼化一体化流程中核心位置,如图6所示。轻石脑油和抽余油直接输送到烷烃脱氢装置,生成的烯烃作为靶向催化裂化装置原料。蜡油、加氢重油直接作为靶向催化裂化装置原料。尤其蜡油是优质的原料,其大分子饱和烃经靶向催化裂化工艺加工,可以高选择性地转化为烯烃,成为低碳烯烃前身物,而加氢重油中的饱和烃除高选择性裂解外,胶质和沥青质转化为焦炭,为靶向催化裂化工艺提供足够的热源。靶向催化裂化装置处理原料油馏程拓展到碳五或碳四馏分,从而可以整合现有的低碳烯烃生产技术,进而缩短炼油与化工一体化流程。
4.3CO2排放近零的靶向催化裂化工艺概念设计
靶向催化裂化工艺具有较高的焦炭选择性,可以控制焦炭产率正好满足装置热平衡需求。焦炭产率低会降低装置的烧焦能力,再借助纯氧再生技术,使再生过程排放的烟气几乎全是CO2。当CO2排放量收费特别高,CO2与H2反应生产甲醇有经济效益时,可采用CO2生产甲醇技术,甲醇作为靶向催化裂化工艺反应部分的原料,这样可以实现靶向催化裂化工艺近零CO2排放。H2可来自烷烃脱氢装置,或者水电解,水电解生成的O2可提供给再生部分。CO2排放近零的靶向催化裂化工艺概念设计见图7。
5结论与展望
环保法规和产品质量要求不断升级以及燃料消费不断减少,传统燃料性炼油厂面临转型发展迫切需求,而以生产汽油和柴油为主的传统催化裂化工艺首当其冲。基于催化裂化工艺加工原料的组成,催化裂化工艺由生产清洁汽油的重要技术逐步成为生产低碳烯烃、BTX?多环芳烃的重要技术,同时成为炼油与化工一体化的能量原料中心。对现有的生产低碳烯烃的蒸汽裂解、催化裂解、烯烃裂解和甲醇制烯烃技术特征进行分析,发现蒸汽裂解和催化裂解工艺存在着乙烯?甲烷收率比过低,且甲烷产率过高,而烯烃裂解工艺原料来源不足,甲醇制烯烃工艺原料主要来自煤制甲醇,造成高碳排放。为此,对催化裂化工艺所涉及的原料、催化剂和催化反应工程进行系统研究,提出靶向生产低碳烯烃的催化裂化工艺,形成如下结论:
(1)将现有的蒸汽裂解、催化裂解所加工的饱和烃原料高选择性转化为烯烃,再以烯烃为原料转化为低碳烯烃,实施C—C键选择性断裂,提高碳原子效率的同时满足低碳烯烃生产方案高效灵活切换。
(2)将现有的催化裂解催化剂活性组元更换为中孔和?或小孔沸石,取代已使用近60年的大孔沸石,以尽可能提供烯烃产物的选择性,使催化剂开发与低碳烯烃生产相适应,实现催化剂技术开发跨越式进步。
(3)深度开发变径流化床催化反应工程技术,将原有的变径流化床两个反应区拓展到3个或4个反应区,同时实现烯烃裂化反应、饱和烃裂化反应、含氧化合物转化反应。
(4)在原料结构、催化剂活性组元和催化反应工程创新基础上,开发出多产乙烯+丙烯+丁烯、乙烯+丙烯、丙烯、丙烯+丁烯4个不同生产技术方案的靶向催化裂化工艺,同时实现4个生产方案之间可灵活切换。
(5)靶向催化裂化装置与烷烃脱氢、烯烃和烷烃分离、烯烃叠合等装置深度耦合,构成新一代炼油与化工工艺流程,实现炼油与化工高度集成,为开发CO2排放近零的催化裂化工艺提供技术基础。